There has been a lot written about how wind power has taken over a lion's share in the energy sector. But there is one subject that hasn’t received as much attention as it should: the property losses of wind turbines. Many (most) people insuring these assets know that there is a dreadful record; the risk isn't as clear-cut as most would like to think when thinking about renewables.
The  trend has been especially pronounced given the rapid growth of wind power in ever complex environments, as well as the increasing frequency of extreme weather events leading to outsized claims.
Much confusion swirls around the actual causes triggering the losses. But before digging into the risks, let's first understand how a wind turbine works.
A turbine is a variable speed, variable pitch machine; it is fitted with a direct-drive, permanent-magnet, synchronous-generator, which is coupled to the grid through a fully rated converter. In plain English, you can think of it as a set of major components that include the foundation, tower, nacelle, rotor, and a bunch of mechanical-electrical components that generate power to the grid.
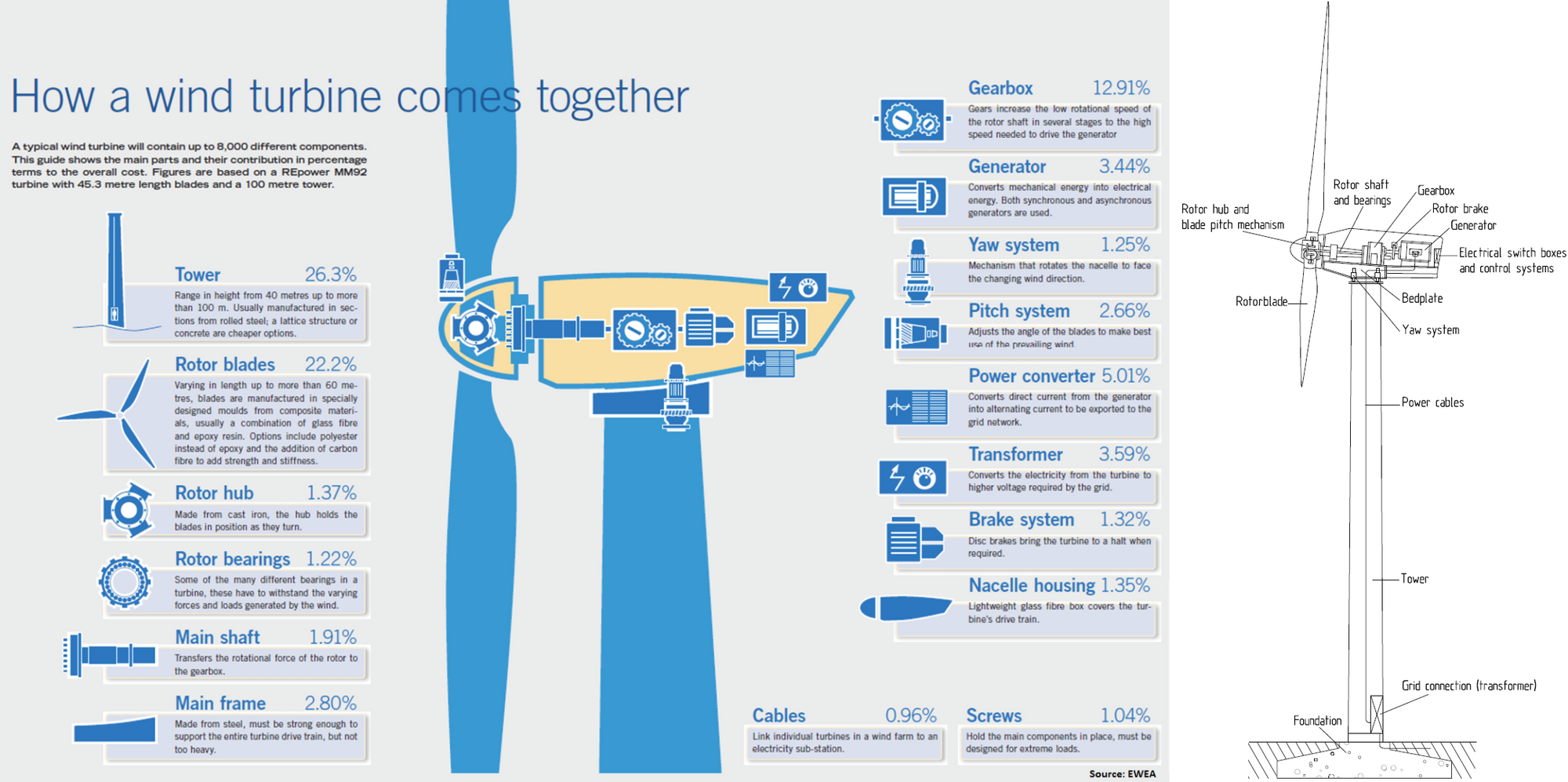
The nacelle is the heart; it includes the drive train (rotating shaft, gearbox, generator, and braking systems), yaw, and control systems. The rotor involves all other rotating parts outside the nacelle, such as the blades, the hub casting, and the blade pitch system. The tower components include the steel plate, access equipment, the electrical system, and internal lighting.
The basic process goes like this: wind impacts the blades causing the hub and shaft to rotate. This rotational energy is converted into electrical energy using a generator. Most, but not all, have a gearbox between the blades and the generator to optimize the speed (frequency) of the power generation.
While the principles are simple, the specific manner in which power is generated is not. Most utility turbines are upwind design, which means the unit turns into the wind using the yaw gears. This rotates the entire nacelle assembly on top of the stationary tower.
A turbine is only designed to operate within a narrow range of wind speeds, however it must orientate into the wind at all times to prevent damage during high gusts. Once the “cut-in” speed is reached, rotation begins and the blades pitch to capture the wind and speed up rotation. At optimum speed, it generates maximum power. The turbine moves the axis of the blades (pitch) to “stall” the rotation and continue power generation within the safe operating limits. If the maximum speed is exceeded, the unit will further pitch to stall the machine’s rotation and apply the rotor lock and braking system to prevent damage to the unit from over speed conditions.
The system is actually more complex when all the monitoring and maintenance systems and practices are accounted for, with a sample depiction shown in the following figure. Â
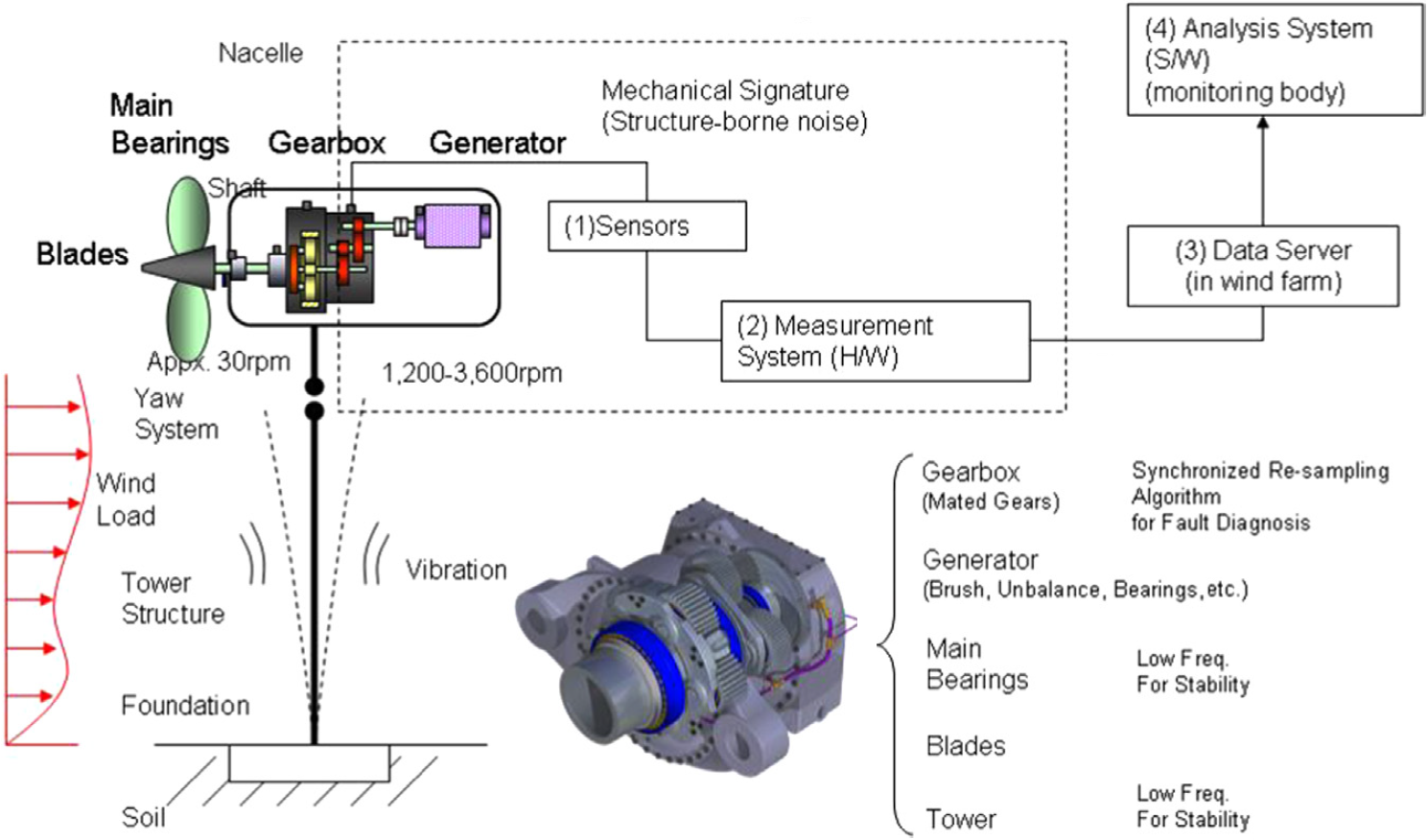
Main Failure Modes
There are many, many, ways a turbine can fail. With more than 8,000 parts on each unit, there's a lot that can and will go wrong.
Turbines are unmanned structures; safety is a function of its ability to meet the structural loads throughout its life cycle, from manufacturing to decommissioning. However, a wind turbine failure is not necessarily contained to a single unit; it poses a threat to the surrounding area.
Some of the main challenges to technical reliability are depicted in the following figure and described below:
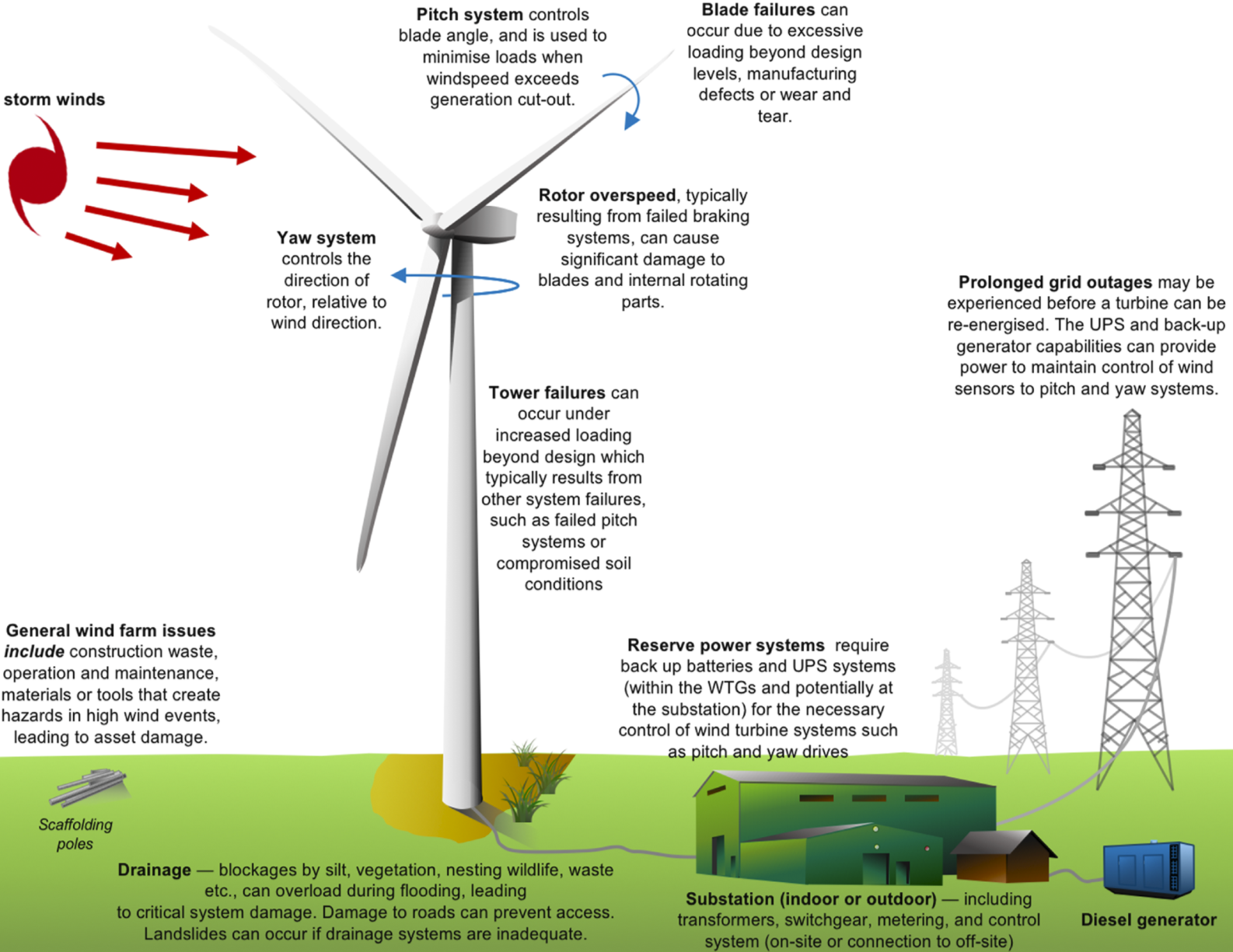
Fire
A wind turbine is made or uses of a variety of materials, some of which are flammable. This includes insulating materials, lubricants for the rotating parts, as well as cladding of the fiber-reinforced plastic in the nacelle. For instance, when polyurethane and plastic (often non-retardant) are used in the nacelle walls, auto-ignition can occur in 12 seconds at a temperature of 335 ÂşC-378 ÂşC.
The ignition sources can be internal such as the electronics and braking systems, or they can be externally caused, such as lightning, hot-work, careless smoking, etc. A typical flame slag has a temperature of 2,100 ÂşC of less than 1 second, which is enough to trigger a fire.
Furthermore, wind turbines generate electrical power at a voltage level similar to that of a power station, and they are the largest rotating machines in the world.
The majority of wind turbine fires occur in the nacelles, making it very difficult to fight the fire once it is out of control. Delayed response time (these things are several meters up in the air) and remote geographic location often result in a wind turbine that is fully engulfed in flames and a total loss.
In addition, during the fire there may be falling debris that is also on fire presenting more hazards to the surrounding areas (remember those wildfires?). For this reason, vegetation, stored material, vehicles and people should be restricted from occupying the area directly at the base of a wind turbine.
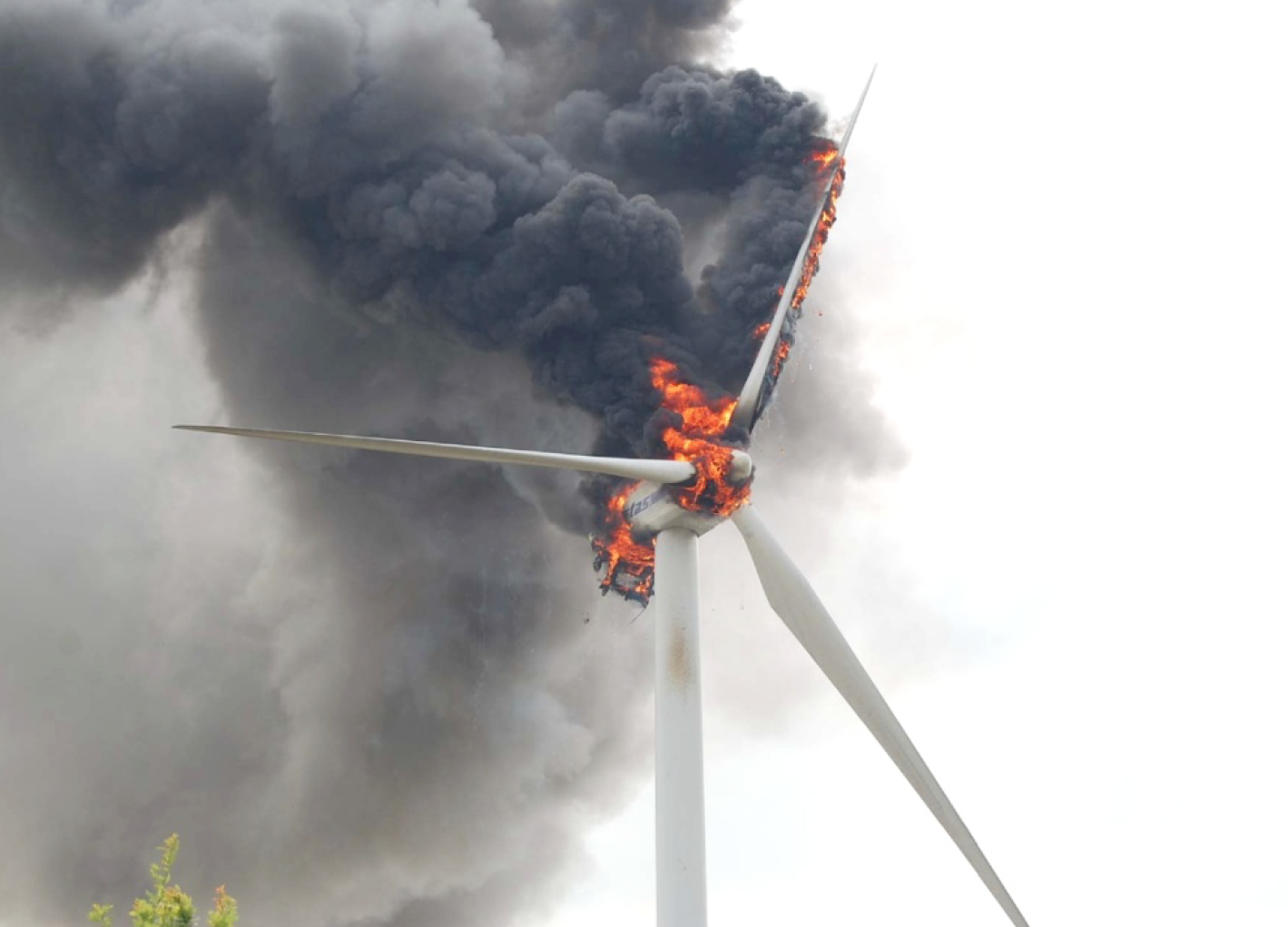
Even if most wind turbine towers and nacelles have smoke detectors, very few are fitted with fire suppression systems. Â This why fire prevention is the only reliable option by ensuring adequate housekeeping, a suitable hot-work program, correct maintenance and inspection practices, among others. Other controls such as confined entry practices with portable fire extinguishers and emergency descend devices are also required, as well as fire drills.
Rotor Brake
This system is designed to bring the rotor to a stop within the shortest period of time under any conceivable circumstance. It is by far the most critical safety system of a wind turbine, which can result in catastrophic failure if it fails.
The mechanical brake on large turbines between the gearbox and the generator is only designed to act as an arresting brake. The rotor stop in these units rely on the blade pith control. It work works by moving the axis (pitching) of the rotor blades towards a feathered position, bringing it to a standstill within only few seconds.
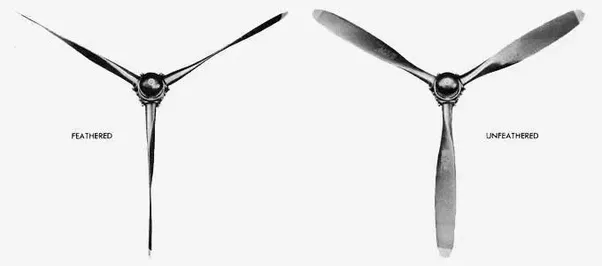
Braking must start immediately with a high pitching rate to prevent rotor overspeed. When the electric generator loses synchronization, the entire rotor power becomes available for accelerating the rotor. Without immediate "braking", the rotor speed rapidly increases and within seconds the rotor can be destroyed by the centrifugal forces (see following video). Falling debris is often noted over a mile from a turbine runaway event.
Structural strength of the rotor system
Despite the advances in monitoring technology, it is  difficult to monitor for structural strength. This is critical for rotating parts, particularly the rotor system. These components can accumulate up to 108 load cycles during a design life of 20-25 years; this makes fatigue a serious matter.
Most rotor blades are made of a fiber-reinforced composite material (polyester or epoxy resin and glass fiber or carbon fiber). If a structural failure occurs, a blade is unlikely to break off abruptly, but would rather wear/frail out. There are normally three root causes of blade failure: defects in design or manufacturing, improper wind orientation of the turbine, and over speed causing centrifugal separation.
Fatigue is most critical on the metal-connecting structures and interfaces between the connecting flange and the blades. If there is an undiscovered and progressive fatigue crack in these areas, the blades can suddenly break off. Anything within two to three diameters of the blades are subject to falling debris. Some wind turbine manufacturers recommend a clear zone of up to 500 meters from the wind turbine base.
Lightning
Wind turbines are a natural attractant for lightning because they are high, slender structures. This results in a high frequency of lightning strikes with the vast majority of the damage concentrated at the tip of the blades.
Today, lightning protection systems are a standard feature. They must be designed to protect the mechanical components from damage, as well as to ensure that the electrical and electronic components are not destroyed or subjected to excessive voltage.
The components primarily affected by a lightning strike are the rotor blades. If the
blades or their spars are made of steel, they will form an ideal lightning conductor and do not need any further lightning protection devices. Otherwise, a metal receptor is located at each blade tip and connected to a thick metallic wire that runs along the interior of the blade to the root. The conductor is connected with flexible metallic strips to the rotor hub and thus to the earthing system of the wind turbine. Regardless of its effectiveness, damage can still occur when there is an interception failure of the air termination system on the blade surface.
Lightning damage includes includes burns, punctures, delamination of the blade structure, debonding of the shells and the detachment of part of the blade, and cosmetic failures such as peeling paint, superficial marks, or slight melting of the air termination system.
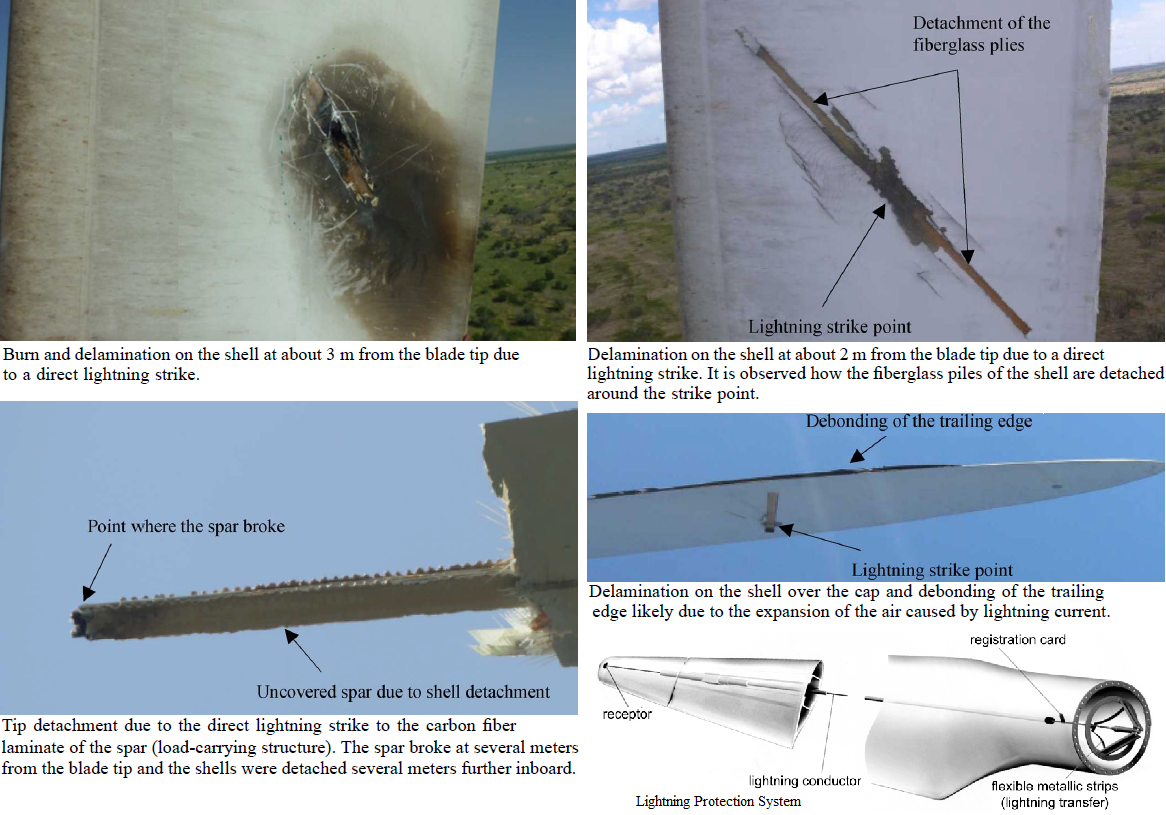
Icing
Icing is a special risk and it can occur on all parts of a wind turbine, especially when the rotor is turning. It is more likely to occur at temperatures around freezing and in environments with high humidity.
The risk of ice accretion is that lumps of ice of considerable weight can be thrown away by the rotating rotor over distances of several hundred meters. This becomes critical when the units are located near sensitive receptors such as buildings and highways. There is a very simple way to prevent ice throws: don’t run a turbine during icing conditions.
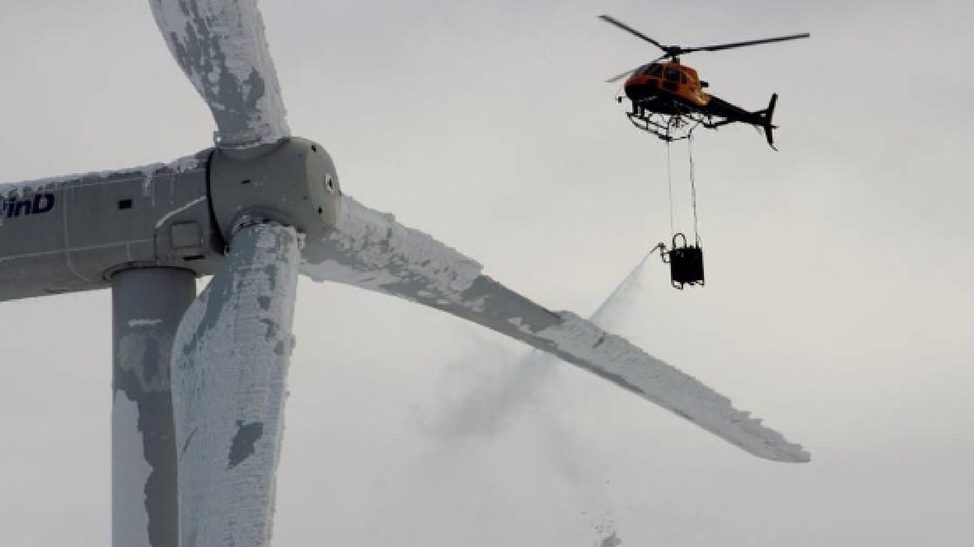
Earthquake
Many wind farm locations in the world have high potential for seismic activity. Â In addition, the low natural frequency of its slender geometry and large mass makes a wind turbine a vulnerable structure under seismic loads.
Share, follow, stay tuned for more!